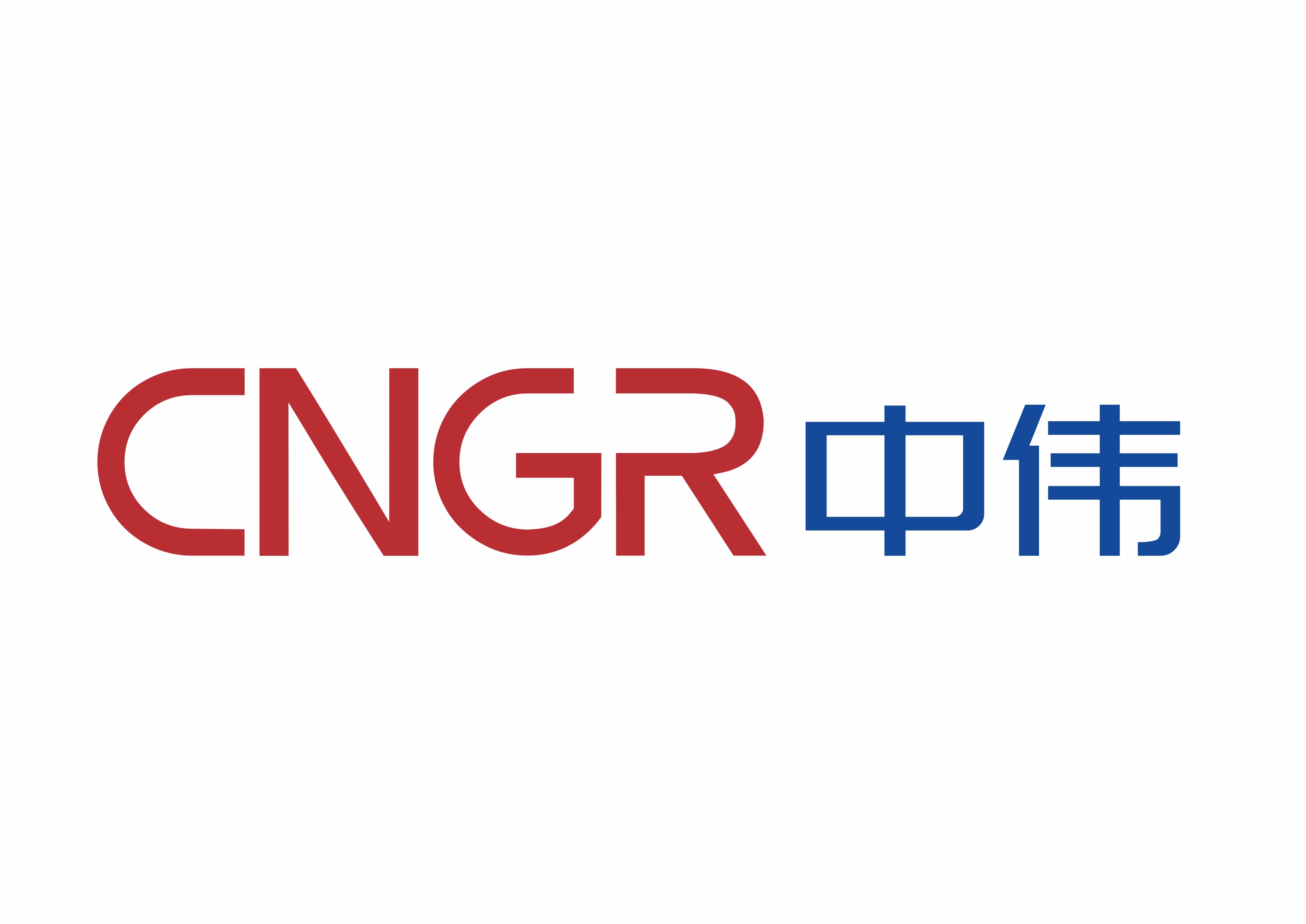
Customer Quaity Engineer - El Jadida
- CNGR Morocco New Energy Technology
- EL JADIDA, Morocco
- 01 JUNE 2024
- Experience of 1 - 3 years
- 01 JUNE 2024
- CDI
Data Statistics:
Data Judgment:
Data Analysis:
Palletizing Arrangement:
System Maintenance:
Summary Report:
Others: